吐絲機與夾送輥
通過夾送輥電流限幅值的調(diào)節(jié),可以改變夾送輥在夾持過程中的工作狀態(tài)及夾送輥夾持能力。應(yīng)控制其產(chǎn)生的夾持力小于壓下力與摩擦系數(shù)的乘積,以使夾送輥圓周速度與線材速度之間的準(zhǔn)確匹配,從而保證良好的吐絲質(zhì)量。
夾送輥的速度一般超過精軋機出口速度的3%~5%,在軋速很高的情況下可以再增大些,但一般不應(yīng)超過10%。夾送輥的速度設(shè)定是由人工向計算機輸入夾送輥輥徑,再由計算機根據(jù)軋制速度和夾送輥超速系數(shù)算出夾送輥的速度計算值,該值即為夾送輥速度基準(zhǔn)值。
夾送輥輥縫設(shè)定范圍為0.2~2mm,視不同規(guī)格和鋼種進行調(diào)整;夾送輥氣缸工作壓力為0.2~0.35MPa,視不同規(guī)格和鋼種進行調(diào)整;夾送輥導(dǎo)衛(wèi)的安裝對中較為嚴(yán)格。進口導(dǎo)衛(wèi)要對準(zhǔn)夾槽,推到位后再夾緊固定。出口導(dǎo)衛(wèi)與夾送輥輥面保持微間隙并夾緊固定
(1)夾送輥前光電管檢測信號失靈,使夾送輥不能按時張開/閉合而造成堆鋼;
(2)夾送輥孔槽與所軋規(guī)格不符,或上下輥錯位造成堵鋼堆鋼;
(3)導(dǎo)衛(wèi)安裝不正確,導(dǎo)衛(wèi)、輥環(huán)磨損嚴(yán)重或?qū)l(wèi)內(nèi)有異物導(dǎo)致堆鋼;
(4)吐絲管內(nèi)有異物、吐絲管變形、吐絲管穿孔或磨損嚴(yán)重引起堆鋼;
(5)夾送輥輥縫或氣缸工作壓力設(shè)定不合理造成堆鋼或拉斷;
(6)精軋機、夾送輥、吐絲機三者速度配合不合理引起堆鋼;
(8)線材內(nèi)部質(zhì)量缺陷(冶煉缺陷)或軋制缺陷(嚴(yán)重折疊)造成堆鋼
在軋制大規(guī)格高線產(chǎn)品時夾送輥升速的作用
在低速大規(guī)格線材產(chǎn)品軋制時,由于尺寸大、速度低,在軋件尾部離開減定徑機后,會由于水冷段的抗力等因素,導(dǎo)致線圈尾部吐絲圈小或扭花,無法吐絲成圈,滯留在吐絲管內(nèi)造成事故。故當(dāng)軋制速度低于22m/s左右時,需要在軋件尾部離開減定徑機時,采用夾送輥和吐絲機升速的控制方式,在其電流限幅值下,以最大允許的加速度,保證軋件的尾部在22m/s這一速度左右完成吐絲。
(1)軋機間張力太大,精軋機、減定徑機的轉(zhuǎn)速波動過大;
(2)水冷段對中調(diào)整偏差,噴嘴導(dǎo)管磨損、腐蝕造成軋件運行不穩(wěn)定;
(3)由于夾送輥輥環(huán)磨損或氣缸連桿機構(gòu)失效導(dǎo)致的夾送輥夾持力不適當(dāng);
(4)吐絲管彎曲曲線的偏差,吐絲管嚴(yán)重磨損,吐絲管氧化鐵皮粘接,吐絲管動不平衡引起成圈差;
(5)減定徑機、夾送輥、吐絲機速度配置不當(dāng),軋機嚴(yán)重的速度波動,引起軋件速度或快或慢,導(dǎo)致線圈大小不均;
(6)吐絲機后的輥道平臺不夠高,當(dāng)軋件溫度高時,線圈太軟,線圈落到接收平臺上,會變成橢圓或亂圈。
吐絲機超前系數(shù)對線圈吐絲狀態(tài)的影響
吐絲機超前系數(shù)的變化,會直接引起線圈直徑大小及布圈偏向的變化,給后續(xù)的集卷造成一定的影響。吐絲系數(shù)過大,會使吐絲線圈直徑偏小同時線圈順吐絲機旋轉(zhuǎn)方向左偏;反之,線圈直徑偏大,同時線圈順吐絲機旋轉(zhuǎn)方向右偏。過大的吐絲系數(shù)設(shè)置偏差,會導(dǎo)致線圈吐絲瞬間失衡側(cè)立,嚴(yán)重偏離吐絲軸心線,圈形不良,甚至無法集卷。根據(jù)不同的規(guī)格及軋制速度,吐絲機超前系數(shù)一般取2%~10%之間。
避免大規(guī)格軋材軋制時吐絲機卡鋼,首先必須保證夾送輥對大規(guī)格線材吐絲尾部的控制能力,這是建立在正確的夾送輥輥縫、壓力、超前量、扭矩、電流限幅設(shè)定基礎(chǔ)之上的,以使軋件尾部能順利吐出。其次,由于大規(guī)格成品孔型側(cè)壓角小、輥縫相對亦小,所以,在保證基本的軋制條件下,必須嚴(yán)格控制住成品在任何時候的飛邊耳子出現(xiàn),這是確保大規(guī)格線材頭、中部不出現(xiàn)吐絲機卡鋼事故的關(guān)鍵。
(1)電機轉(zhuǎn)速波動大造成機體振動,應(yīng)進行電機優(yōu)化或優(yōu)化軋制工藝;
(2)聯(lián)軸器不對中或螺栓松動造成振動,應(yīng)重新進行對中找正,其徑向偏差不應(yīng)超過0.1mm;
(3)齒輪箱內(nèi)軸承損傷或間隙偏大造成振動,每年應(yīng)解體檢查軸承間隙是否符合標(biāo)準(zhǔn);
(4)齒輪箱內(nèi)傘齒輪調(diào)整不當(dāng),嚙合差造成振動,應(yīng)保證齒側(cè)隙0.2~0.4mm,嚙合面大于20%;
(5)吐絲錐幅板開裂或動不平衡造成振動,應(yīng)定期檢查吐絲錐是否開裂,動平衡塊是否丟失,并將吐絲管、吐絲盤安裝好后做動平衡;
(6)吐絲錐、吐絲盤與圍盤間隙超差造成振動,當(dāng)間隙小于2mm時,會因吐絲錐發(fā)熱導(dǎo)致吐絲盤與圍盤摩擦,應(yīng)對圍盤進行修磨,當(dāng)間隙大于4mm時,會導(dǎo)致間隙內(nèi)卡鋼,從而引起吐絲錐及機體損傷;
(7)吐絲管動不平衡造成振動,吐絲管重量、材質(zhì)、壁厚不規(guī)范,吐絲管彎曲曲線不規(guī)范,吐絲管管夾安裝不規(guī)范,吐絲管嚴(yán)重磨損或氧化鐵皮粘接,均會導(dǎo)致動不平衡,應(yīng)及時更換吐絲管。
由于高速線材軋機的高速軋制,普遍采用了設(shè)計有一定傾斜度(其軸線與水平夾角為10°~20°)的臥式吐絲機,為了防止氧化鐵皮停留在吐絲管內(nèi),以及形成吐絲管內(nèi)壁的“刻痕”。在吐絲管的入口端裝有高壓空氣吹掃噴嘴,依靠它對吐絲管進行吹掃,有利于減緩?fù)陆z管的磨損,并加強吐絲管的散熱性能,延長吐絲管的使用壽命。空氣的供給,可以在線材尾部離開精軋機或減徑定機前被釋放,或由操作人員確定吹掃時間,或連續(xù)吹掃。
降低輥耗的有效途徑——采用表面堆焊技術(shù)修復(fù)夾送輥
邯鋼薄板坯連鑄連軋生產(chǎn)線于1999年12月10日投產(chǎn)使用,是國家引進德國西馬克公司研究開發(fā)的20世紀(jì)90年代世界鋼鐵工業(yè)高新技術(shù)CSP(CompactStripProduction即緊湊式板帶生產(chǎn))生產(chǎn)線之一,是國家“九五”重點工程之一。夾送輥系統(tǒng)作為CSP生產(chǎn)線中重要的一環(huán),其設(shè)備運行是否正常與平穩(wěn)直接影響到整條CSP生產(chǎn)線的穩(wěn)定、均衡生產(chǎn)。為了更好的保證生產(chǎn)、降低成本,許多關(guān)鍵件急需國產(chǎn)化改造,夾送輥就是其中重要的一項。
夾送輥承受的溫度約為550~650℃;要求夾送輥輥面具有耐高溫、耐冷熱交變的性能。
夾送輥壓力設(shè)定值最大為40kN左右;要求在線生產(chǎn)時夾送輥輥面承受最大壓力設(shè)定值運行不低于10個周期(6萬噸/周期)。
帶鋼咬入夾送輥輥縫時瞬間沖擊力非常大,要求夾送輥輥面承受500~600kN瞬時沖擊而不受損傷。
要求夾送輥過鋼量達到60萬t后,輥面直徑方向磨損量≤35mm。
要求夾送輥輥面耐高堿度循環(huán)水反復(fù)沖蝕冷卻。
夾送輥制造完成后必須做動平衡試驗,平衡精度等級要求為G6,提交動平衡試驗報告。
夾送輥是CSP生產(chǎn)線后部卷取機械的重要組成部件之一,其作用為在開始卷取時咬入帶鋼,使帶鋼頭部向下彎曲并沿導(dǎo)板方向順利地進入卷桶,并建立卷取操作所需的張力。上夾送輥為空心輥焊接結(jié)構(gòu),下輥為實心;上、下夾送輥均為硬質(zhì)耐磨表面,冷卻方式均為外水冷卻方式。
熱連軋夾送輥承受400℃以上鋼帶高速沖撞和甩尾打擊,而且輥子與鋼帶之間相對速度差時有發(fā)生,因此夾送輥損壞失效行為主要為磨損、粘鋼和局部小塊剝落。其中粘鋼是由于相對速度差引起的粘著磨損。
選擇科學(xué)的堆焊方法極其重要,主要考慮幾個方面的因素:夾送輥的質(zhì)量要求、基體金屬的冶金性能、耐磨堆焊合金層的形成、工藝操作技巧及修復(fù)成本。
(1)選用耐磨合金焊條,手工堆焊,生產(chǎn)時間較長,保溫不好,易出現(xiàn)氣孔、夾渣,隨著堆焊厚度的增加,焊條頭較多,浪費大,成本增高。
(2)選用明弧焊堆焊,不僅成本高,而且明弧焊絲在焊后一般硬度及耐磨度均偏低,難以確保夾送輥的使用壽命。
(3)采用管狀藥芯焊絲埋弧堆焊,焊絲藥芯成分可根據(jù)輥面技術(shù)要求調(diào)整,埋弧堆焊焊道成形好,夾渣較少,成本較低,但易出現(xiàn)氣孔。根據(jù)以上分析,最終使用管狀藥芯焊絲,采用埋弧堆焊的工藝方法。
夾送輥堆焊材料應(yīng)選擇具有較高的硬度和較好的塑韌性,抗磨料磨損性能好,輥面易生成較致密且附著性好的氧化物薄膜,在國外,此類堆焊材料大多為Cr-Mo型低合金鋼和Cr13型馬氏體-鐵素體型不銹鋼,堆焊層硬度一般控制在53HRC+2HRC。
研究對比國內(nèi)外堆焊輥的相關(guān)資料如下:若選擇日本神戶制鋼所或美國麥凱公司生產(chǎn)的夾送輥專用焊絲,焊劑價格高昂,而且相對配套的各種設(shè)備要求高,工藝方法要求嚴(yán)格,若選擇與國內(nèi)知名焊材生產(chǎn)廠家共同研發(fā)藥芯焊絲,不僅價格便宜,而且適應(yīng)目前國內(nèi)現(xiàn)有的設(shè)備來操作,工藝方法簡單易行,為此根據(jù)選擇焊材思路及國外焊材主體成分資料與上海焊材廠家一起反復(fù)研究,經(jīng)多次試驗最終確定了焊絲焊劑成分及合理配比。
根據(jù)焊接材料及工藝方法的最終確定工藝路線為:夾送輥粗加工-超聲波探傷-預(yù)熱-管狀焊絲堆焊-焊后熱處理-精加工-堆焊金屬表面硬度檢驗-超聲波探傷-動平衡實驗-裝機使用。
輥子表面所有氧化物和疲勞金屬層(邊緣上的冷變形),都必須用適當(dāng)方法去除,以保證有較好的表面進行堆焊,如準(zhǔn)備不當(dāng),會引起氣孔,稀釋率高,涂層與基體的結(jié)合強度差。采用機械切削的方法去除輥子在使用過程中形成的疲勞層及缺陷,根據(jù)現(xiàn)場磨損狀況調(diào)整加工要求,直到去掉所有的疲勞層及局部缺陷。
對輥子進行全面的著色和超聲波探傷,根據(jù)檢測報告采取相應(yīng)措施。
(1)在輥子焊前、機加工前對輥頸、輥身進行超聲波和探傷,以判別輥子的修復(fù)價值。
(2)對車削后輥面進行探傷檢測,檢查疲勞層、裂紋等缺陷是否已徹底清除,(此工序可能反復(fù)進行),直到輥子的修復(fù)前狀態(tài)符合探傷的相關(guān)標(biāo)準(zhǔn)
(3)對堆焊層是否存在裂紋、夾渣和氣孔等缺陷進行探傷檢測;對輥頸重新檢測,檢查在輥面堆焊加工過程中對輥頸部位是否產(chǎn)生影響,并出具報告,隨產(chǎn)品一起交付用戶單位。
針對夾送輥在堆焊過程中的預(yù)熱、中間及最終熱處理的需要,熱處理爐在保證爐膛容積、熱處理功率及溫度控制等方面應(yīng)達到大型輥類熱處理工序使用要求。
輥子預(yù)熱對保護金屬不引起開裂和變形是一個十分重要的因素,恰當(dāng)?shù)念A(yù)熱可使輥子堆焊前充分地膨脹,這樣在焊接結(jié)束后,焊層與基體的變形、應(yīng)力為最小,設(shè)計預(yù)熱溫度為400℃,保溫2h.。
在堆焊過程中,用氧乙炔火焰或電加熱板對輥子進行加熱保溫,層間溫度控制在280~300℃范圍內(nèi)。
輥身堆焊后加熱到560℃,保溫一段時間后隨爐冷卻至室溫?;鼗鹛幚砗?,消除焊接產(chǎn)生的內(nèi)應(yīng)力。
為恢復(fù)輥身尺寸及相應(yīng)的力學(xué)性能,堆焊是整個夾送輥修復(fù)工藝中最直接影響輥子材質(zhì)、尺寸、形狀、內(nèi)在質(zhì)量的關(guān)鍵工序,通過使用兩臺MZ-1000埋弧焊機和大型焊接轉(zhuǎn)胎實施焊接,連續(xù)焊接長達7~8天(每天24h),節(jié)約2~2.5t堆焊材料。
堆焊過程中,加強現(xiàn)場檢測工作,通過量具、儀器、儀表的使用,時刻掌握影響焊接質(zhì)量的各類因素,如溫度、電壓、電流、送絲速度及輥子旋轉(zhuǎn)速度等等。
通過有效的控制,嚴(yán)格執(zhí)行工藝參數(shù),使同時使用的兩臺埋弧焊機處于幾乎相同的工作參數(shù)條件下,確保焊層的統(tǒng)一性能。還通過精確計算材料用量,在同一根輥子上使用某廠家同一批號的焊絲,保證材質(zhì)均勻性,取得較好的焊接效果。
電壓:28~34V;電流:500~600A;焊絲伸出長度:28~31mm;輥子線速度:500~700mm/min;導(dǎo)前距:50mm層間溫度:280~300℃;送絲速度:0.2r/s;輥道搭界率:50%。
(1)對輥身分六點進行輥身直徑尺寸檢測,符合圖紙尺寸。
(2)對輥面按A,B,C,D四條母線進行硬度檢測,相鄰母線間剖面夾角為90°,每條母線上測10點硬度值,硬度值均為大于51HRC,小于54HRC。
(3)經(jīng)過由資質(zhì)探傷檢測單位對輥身按標(biāo)準(zhǔn)進行探傷,確認輥面堆焊層中沒有超標(biāo)缺陷及裂紋性缺陷。
(4)按圖紙要求請專業(yè)廠家對夾送輥做減重法動平衡試驗,達到G16級。
大幅度降低了輥耗,提高了軋機產(chǎn)量、作業(yè)率及產(chǎn)品質(zhì)量,達到了進口輥使用前標(biāo)準(zhǔn),實現(xiàn)了夾送輥修復(fù)前的預(yù)期目的,2004年~2005年公司共修復(fù)4套夾送輥,累計過鋼量260萬t。
隨著堆焊技術(shù)的推廣使用,各生產(chǎn)企業(yè)為降低成本,將原單純的更換配件傾向于修復(fù)配件,夾送輥的整體堆焊修復(fù)在備件效能優(yōu)勢凸現(xiàn),修復(fù)的價格一般在新產(chǎn)品價格的25%~35%,夾送輥的直接經(jīng)濟效益見表。
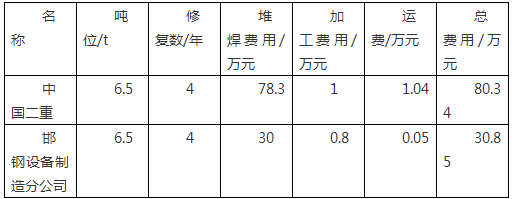
采用表面堆焊技術(shù)修復(fù)夾送輥,經(jīng)實踐證明:堆焊夾送輥所選用的工藝,配定的硬面層堆焊材料是可行且可靠的;經(jīng)修復(fù)的夾送輥使用壽命大大提高,滿足連軋廠生產(chǎn)需求;節(jié)約了大量企業(yè)制造費用、運輸費用、外部資金,效益顯著。
2022/07/05 15:35:33
621 次