冷軋軋制油的選擇及原理
冷軋軋制選擇軋制油是否正確,直接影響到軋機的產量和質量. 特別是新建的軋機, 必須選擇合適于軋機特點的冷軋油, 才能滿足軋制規(guī)范和后部工序的要求. 本文根椐武漢鋼鐵公司冷軋廠五機架軋機, HC軋機及寶鋼五機架連軋機組的一些經驗和數據, 提出適合于循環(huán)系統(tǒng)的冷軋軋制油潤滑特性和退火清凈性的要求。
無論是原有的軋機或是新建引進軋機, 都有一套滿足產品大鋼的軋制規(guī)范, 都有一個最小的軋制厚度, 要滿足該軋機能順利的生產出最薄的厚度, 必須有相應的具有一定潤滑性的冷軋油.體現冷軋油的潤清性的一個重要指標是該油品的皂化值, 皂化值越高, 冷軋油的潤滑性越好. 但一般來說, 合成酯系列的油品的價格也越高, 因此必須合理侈選擇冷軋油的潤滑性。
冷軋時變形區(qū)中的摩擦系數與冷軋油的潤滑性, 亦就是與油品的皂化值有一定的關系. 皂化值越高, 其在變形區(qū)中的摩擦系數越小, 而摩擦系數的大小直接決定了該軋機所能軋制的最薄厚度。
根據冷軋帶鋼彈性核理論[1], 冷軋帶鋼時, 在變形區(qū)中, 金屬可出現得不到壓下而轉入彈性狀態(tài). 并處于變形區(qū)的中心部分, 故稱彈性核. 彈性核的出現徒然消耗軋制壓力而不產生壓下變形, 是延伸困難的根本原因。
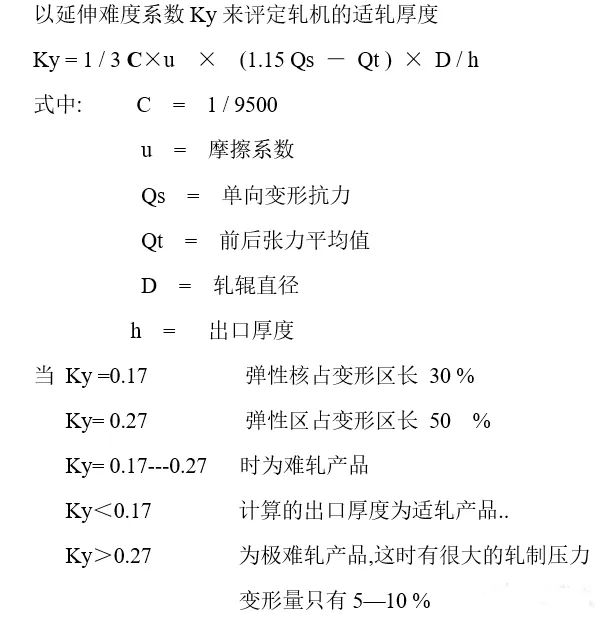
以上式可以看出, 最小軋制厚度與摩擦系數u 和輥徑 D成正比. 對于一定的軋機, 軋制定材質的帶鋼時, 摩擦系數越小, 則該軋機可軋厚度就越薄. 這就取決于使用怎樣潤滑性的冷軋油產品。
根據武鋼五機架冷連軋機組生產實踐, 軋制難軋的最小厚度及適軋厚度, 可以計算出摩擦系數與冷軋油的皂化值有一定的對應關系。
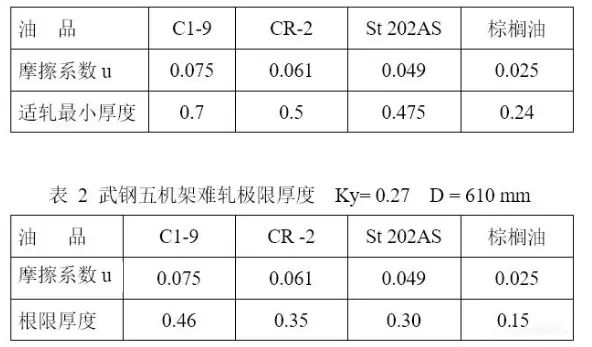
從上述圖, 表可知皂化值每增加 40 mgKOH/g ,摩擦系數約下降0.012---0.014.
武鋼HC軋機設計軋制程序中所用的摩擦系數為0.036 .而根據上述理論計算為 0.033 兩者結果非常接近. 寶鋼五機架冷連軋機組現使用皂化值為 130---160 mgKOH/g的冷軋油. 其模型計算的摩擦系數u
上述計算模型中的摩擦系數取值(光面輥)和皂化值所取值0.049 非常接近. 因此從彈性核理論與皂化值的關系可以估算出一定的軋機軋制一定材質帶鋼的適軋厚度和難軋厚度. 反之, 根據新的軋機, 一定的軋制規(guī)范可較正確地選擇一定潤滑性的冷軋油. 但由于在生產中, 軋機設備經窮有漏油現象 該雜油進入乳兆液腐環(huán)系統(tǒng), 使原有冷軋油的皂化值呈線性下降.因此所選用的冷軋油的皂化值要比理論計算值擴大 10—20 %。以免由于雜油影響冷軋油的軋制性能。
雖然是同樣的皇化值的冷軋油其潤滑性還是一定的差別. 如圖3所示. 皂化值為200mgKOH/g 的棕櫚油與豬油相比, 棕櫚油的潤滑性優(yōu)于豬油. 同樣地在純棕櫚油或者純豬油中添加3—5%的油性劑后其潤滑性要比純油脂的優(yōu)良得多. 因此對同樣皂化值的冷軋油必須進行綜合評定來選擇更滿足工藝條件的冷軋油.
用上述方法來選用冷軋軋制油. 不適用于廿輥森吉米禾軋機. 因泛軋油的潤滑性太好, 易造成輥系打滑. 一般用于20輥森吉米爾軋輥的冷軋油皂化值<95mgKOH/g.
但如果軋后帶卷不經電解脫脂直接在罩式退火爐中緊卷退火, 那么對冷軋油有更高要求, 即具有良好的退火清凈性, 該種軋制油稱” 軋機清凈鋼板(MCS)軋制油. 特別是3---5%H2 ,95—96% N2作為保護氣體的罩式退火爐更是如此. 一般來說全氫爐的退火鋼板表面要清凈一些.
MCS軋制油必須具有較低的揮發(fā)溫度, 良好的抗氧化, 熱劣化性能, 退火后板面的漫反射率≥70% -----使鋼板表面的污垢復制于無色的透明膠帶上, 將這膠帶貼在白色的硬紙上, 用反射法測量亮度(y值). 以無污空白膠帶為100%來表示百分率 (經電解脫脂過的退火帶鋼表面的漫反射率為95%)
乳化液理化性質的變化是由于乳化液中發(fā)生物理和化學變化造成的. 在物理變化中會產生細粒污染, 大都由于細鐵粉在軋輥和帶鋼上擦落產生的. 化學變化是用于變形區(qū)中的變形熱和摩擦熱, 在鐵粉觸酶作用下促進了油膜的氧化, 并使油膜的油質分解成羰基, 羰基與鐵粉生成鐵皂而形成油污. 同時鐵皂也會分解變質與鋼板表面反應產生氧化膜, 因此化學反應生成油污是由于使用的軋制油的氧化物劣化產生的.鋼板表面的氧化膜及其上面的附著的油污直接影響冷軋板的退火清凈性.
在罩式退火時邊緣炭的產生是由于帶鋼邊緣部位接觸保護體的軋制油, 氧化還原. 或炭的析出而變色. 這種邊緣炭的生成不僅有最適宜的溫度, 而且加熱時溫度梯度亦是一個重要原因.軋制油在高溫揮發(fā)成低碳氫化合物及一氧化碳, 二氧化碳等. 一氧化碳就與鋼板表面反應;
3Fe +4CO ------- Fe3O4 + 4 C
即生成了炭. 炭的析出量在500—600C 時具有極大值. 特別是在軋制時產生的微細的鐵粉附著在鋼板表面, 增加了Fe的表面積, 促進了邊緣炭的產生。
含碳量在0.02% 以上, 特別是含Si的低碳鋼在650---700 C 數小時以上加熱時 , 碳從表面析出, 成長為結晶良好的石墨, 影響黑灰的因素有溫度 ,時間 ,帶卷張力 ,保護氣氛, 鋼中含碳量, 表面成份偏析. 另外軋制油在高溫時揮發(fā)成甲烷, 乙烷等低碳化合物進一步的分解仍能析出碳. 因此, 如果在退火肘, 在低溫保溫一段時間, 并增加保護主體吹洗時間, 有利于軋制油的揮發(fā), 可以減少黑灰的產生。一般而言, 隨著冷軋油的皂化值的增加, 退火清性要降低,隨著科技的發(fā)展 , 目前已經應用軋制油皂化值為160mgKOH/g, 仍具有不經電斛脫脂直接退火的良好性能.如武漢陽泰公司 CRD系列軋制油。
冷軋油直接影響到軋機的產量和質量. 使用適當的冷軋油必須滿足軋機的工藝潤滑及其后部工序, 利用彈性核理論求得摩擦系數與冷軋油的皂化值之間有一定的關系,可以合理選擇冷軋油, 如果軋后無電解脫脂機組則必須使用”軋機清凈鋼板” ( MCS ) 軋制油。
用以上方法適合于選擇軋制用冷軋普碳鋼系列的軋制油, 不適用于20輥森吉米爾軋機。
2022/07/21 09:41:52
503 次