High speed wire mill roll selection
I. Introduction
In the middle of the 20th century, due to the war and post-war reconstruction, industrial countries needed a large amount of wire, which promoted the rapid development of wire mill. In the 1960s, the advent of high speed torsion-free wire finishing mill and Stilmore controlled cooling process pushed the world wire production technology to a new stage.
In 1987, the production line of Ma Iron and Steel high-speed wire was built and put into operation, which marked the farewell of Chinese wire production and "double double", and the road to common development of high-speed, torsion-free world. Then, the equipment level and rolling technology of the rolling Mill have changed fundamentally, and the high-speed rolling Mill becomes the main stream of line production in our country.
2. Roll selection of high-speed wire mill
The high speed wire mill has the characteristics of fast rolling speed, high precision, good surface quality, heavy rolling plate, and no torsion or slight tension in the whole rolling line. High speed wire rolling mill is composed of roughing mill, middle mill, prefinishing mill and finishing mill. Generally, the whole rolling line ranges from 28 to 30 pieces.
Roughing mill set is generally composed of 4~8 frames. Because of high rolling temperature, large section and deep groove of roll, the rolls used for roughing mill stand should have good cracking resistance, heat crack resistance, wear resistance and good biting performance. Generally, the roughing mill stand uses pearlite nodular cast iron rolls with HSD 45-55 or alloy semi-steel rolls with HSD 45-50.
The roll of middle mill unit is generally required to have good wear resistance and surface roughness resistance, and there is no great difference in material selection. Therefore, it is economical and practical to use pearlite nodular cast iron roll with hardness of HSD 60 ~70 or alloy infinite chilled nodular cast iron roll in high speed wire rolling mill.
The prefinishing group of high speed wire mill can reduce the rolling accidents and improve the dimensional accuracy of finished wire mill. Therefore, the principle of selecting roll materials for the pre-finishing mill group should be that the rolls used for the unit can play the role of connecting the past and the future, and the wear resistance of the rolls should be the main criterion.
Foreign high-speed wire mills have a wide selection of materials for the roller rings of the prefinishing mill group. Some manufacturers use tungsten carbide carbide roller rings. Although the wear resistance is good, the strength is low and the fracture will occur. The wear resistance of centrifugal composite ring and high nickel-chromium platinum infinite chilled cast iron with rolling ratio is 3 times higher, the strength is higher than tungsten carbide carbide carbide roller ring, and the price is lower. Therefore, centrifugal composite ring and high speed steel roller will be the first choice of roller or roller ring materials in the future prefinishing mill group.
The finishing group of high speed wire rolling mill is an important factor to ensure the high precision rolling of wire rolling mill. Therefore, tungsten carbide carbide roller ring must be used in the finishing group of high speed wire rolling mill, otherwise the rolling speed and wear resis
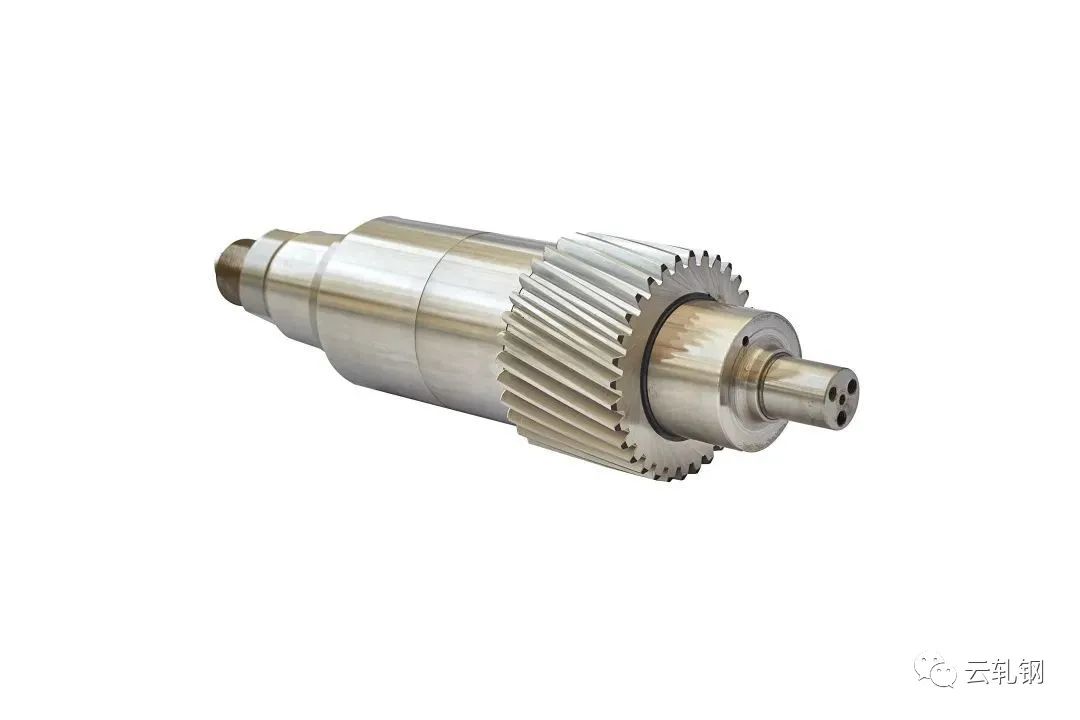
tance of the roller ring cannot be guaranteed. Up to now, there is no material that can replace the tungsten carbide roller ring in the finishing group of high speed wire mill.