Exploration and application of high-speed wire on-line automatic tail-cutting function
Abstract:The tail of the high-speed wire is always cut manually before the Stellmore cooling line reaches the coil collecting cylinder. The feasibility analysis and demonstration of automatic cutting of the tail of the wire are carried out by using a robotic arm, and the practical exploration of automatic tail cutting is realized by explaining the installation, commissioning and initial use of the equipment on site. It provides a useful reference for many high-speed wire production lines in China.
At present, the country has more than 600 high-speed wire production lines, high-speed wire production lines are characterized by high wire speed, generally about 80-120m/s; Continuous production, fast pace, high production efficiency. Due to process characteristics and user requirements, part of the head and tail of the wire must be cut before bundling (the size of the head and tail, ear shape, or the part that cannot meet the requirements of downstream customers due to factors such as non-penetration strength). The cutting of the end of the wire varies with the equipment of the production plant, the common is the small size (less than 8mm) the end of the wire is manually cut on the STELMOR roll line, and the head and large size (8mm and above) the end of the wire is manually mechanically assisted cutting on the P&F line. Due to the factors determined by the process equipment, the tail shear of the wire is carried out on the C-shaped hook at the tail-cutting station of the P&F line after the reel collection. Because the tail of the wire is on the closed side of the C-shaped hook, it is impossible to cut a single point and move out the multiple loops, and the tail rings must be cut at each turn of the multiple loops to achieve the removal of the tail rings after the shear. As we all know, the wire P&F line system in addition to providing the production line with coil transportation, head shear, tail shear, bundling, weighing, unloading and other station functions, another important function is to achieve the cooling and cooling of the wire. The production of large size wire has the characteristics of fast rhythm, high temperature of wire coil and large output. Therefore, the P&F line end shear station of large production lines has always existed "two big and one high" problems, such as heavy workload, heavy physical labor intensity and high ambient temperature.
The purpose of the intelligent construction of the online automatic tail-cutting function is to achieve people-oriented, effectively improve the working environment of employees, reduce the labor intensity of employees, and maintain safe and efficient production of the production line. This paper introduces the automatic cutting of large size wire production line by intelligent control robot on STELMOR roll line.
2、Feasibility analysis
The development of industrial automation and intelligent technology provides conditions for the replacement of manual work by robots in steel rolling production lines. More and more people think that the positions with complex environment and heavy manual labor are replaced by robots. It is of great significance to demonstrate the feasibility of STELMOR online automatic robot tail cutting to replace the artificial mechanical assisted tail cutting on P&F lines.
2.1Work space and environment
The design of large-specification high-speed wire production line generally takes full account of the equipment requirements for high-end wire product production. The design of STELMOR roller table has the characteristics of large adjustment room and large reserved space. The robot tail-cutting equipment is added online, and there is no limit on the working space.
The position of the robot is added in the last section of the STELMOR roller table, and the maximum ambient temperature of various specifications and steel grades during the robot operation does not exceed 250℃, which is the allowable operating temperature of the robot.
2.2The rhythm of production and operation is connected
High-speed wire production line has the characteristics of continuity and fast rhythm, and the steel output interval during normal production is generally about 3.5 seconds. Therefore, the maximum time required for the robot to pull from the tail to the shear completion should not exceed 3.5 seconds. The response time of the robot system is ms level, the two robots have synchronous starting space when coordinating, and the combining time of the two robots is controlled in the space of the steel drawing interval period.
2.3Treatment of the tail material after cutting
For large and medium size production line, the finished product tail spinning ring comparison rules, whether it is online collection after cutting STELMOR roller, or after cutting with the mother part or with the next head into the cylinder collection, there are feasible ways, users can choose according to the actual working environment or working habits of the production line.
2.4Cut the delivery of unsuccessful messages
After the end of the wire is cut on the STELMOR roller table, the end cutting post is no longer set on the P&F line at the back. However, the success rate of robot online cutting is difficult to achieve 100%, once there is a line reel with unsuccessful tail cutting, it must be made up by the post of the rear cutting head to prevent the tail from leaking into the user. Therefore, it is one of the problems that must be solved how to convey the unsuccessful information of robot online cutting to the personnel in the cutting position in time. If the production line chooses to cut the tail material together with the next piece of head into the barrel for collection, that is, the on-line cut tail material hangs on the head of the next roll of C-hook, and the operator of the P&F line cutting head position will take the head of the last piece of material out of the C-hook for collection. If the operator does not get the end material, it means that the last finished product has not successfully cut the end, so it must be made in the reserved end cutting station. This shows that cutting unsuccessful message transmission can be achieved.
3、Equipment installation and commissioning
3.1Equipment selection and installation
A rotating bracket is installed above the Stilmore roller table in the wire production line, and two detectors are installed above the bracket. At the same time, two manipulator devices are installed beside the roller table, one manipulator is equipped with a material stopper, and the other manipulator is equipped with a hook and shear device. The hook material is driven by the cylinder, and the shear is driven by hydraulic pressure (see Figure 1).
When the high-speed wire is in normal production, the speed of the Stelmore roller table is not more than 1.5m/s, the steel crossing interval is not less than 3.5 seconds, and the wire is transported through the Stelmore roller table after being looped by the wire spinning machine. When the tail of the wire passes the detector position, the detector sends a signal to the two manipulators, and the stopper manipulator and the hook cutting manipulator delay the action after receiving the signal. Run to the working position, the stopper drops so that the coil tail remains stationary, the coil is separated in the roller table, and then the hook device on the hook cutting machine hand drops, the stop device rises, the coil advances into the hook device, the hook device lifts the wire to the cutting device blade, and then cuts the wire. After the shearing action is completed, the cut end material is placed in the roller table.
The device is the first set of wire online automatic tail-cutting equipment trial-produced in China, which was installed in April 2019. After several improvements, the hot load commissioning began in July.
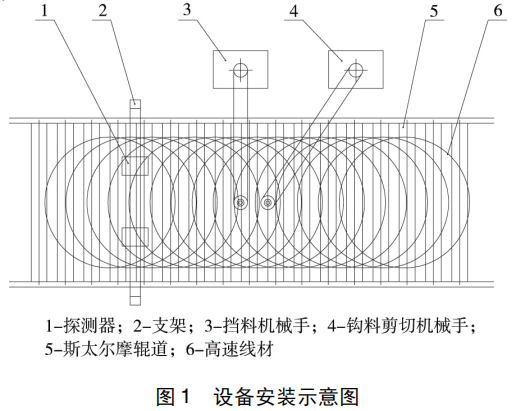
Because it is the first set of intelligent automatic cutting device in China, from the point of view of protection equipment, developed a heat engine debugging program, the debugging period of steel interval from 15 seconds, gradually shortened to the current 5 seconds, but from the rolling interval of 3.5 seconds goal, there is a gap of 1.5 seconds, is currently working with the equipment supplier to develop a debugging program, further optimization.
4、Problems and solutions
The debugging of the first intelligent automatic cutting device in China has exposed some problems. Through problem analysis and research, some problems have been dealt with, and some problems are still improving.
4.1The two-node cluster does not work
During debugging, the stopper manipulator and hook cutting manipulator do not act at the same time, which is mainly caused by the non-reaction or reaction timeout (set 2s) of the laser detector at the tail of the coil. Through inspection and delay adjustment has been resolved.
4.2The cutting was unsuccessful
Shearing failure includes no hook to the material, hook double material, no cutting, etc., mainly related to the delay setting of the stopper manipulator and the failure of the cutting manipulator blade, which is solved by delay adjustment and blade replacement.
4.3Reverse fork material
This phenomenon refers to the phenomenon that several coils of wire coil at the end of the base metal appear to be looped and crossed after the hook cutting manipulator cuts. Because of the looped and crossed, it is very easy to produce a stuck steel accident when the wire coil enters the collecting drum. The main reason for the fork fork is that when the hook material is lifted and cut by the hook material cutting manipulator, the lift height of the hook material is too high, and the delay time of the shear action after the hook material is too long, so that several coils of the tail of the base material are pulled apart, and the elastic force becomes larger. When the tail springs back after the lift shear, it is not recovered in situ, but is misplaced, resulting in the fork fork phenomenon. The treatment method is to adjust the lifting height reasonably and shorten the delay time of the shear action after the hook material.
4.4The number of shear turns is unstable
There is a clear standard in the process of wire reel tail shear coil number, but it is found that the finished product shear coil number is not stable during debugging. If the number of shear cycles is unstable, a small number of shear cycles may lead to finished product quality problems, and a large number of shear cycles will cause a decline in the yield index. The number of shear turns of the device is calculated by laser detector signal, STELMOR end roller speed and stopper manipulator action delay time. Due to the influence of detection sensitivity, response sensitivity and tail spinning state, the calculated number of loops is not in good agreement with the actual number of loops. In the next step, in order to set the action time of the stopper manipulator, in addition to automatically collecting the speed of the R end roller table, the robot system should also be connected with the production PLC system to automatically collect the tail spinning line speed when the shearing coil is spun, so as to accurately calculate the number of tail cutting laps.
4.5Material tracking system integration
The automatic cutting system has a complete fault recording system, and the wire production line also has a complete online material tracking system. The message of failure to cut temporarily depends on whether the cutting operator obtains the end material on the C-hook. However, after the automatic cutting system is integrated with the online material tracking system of the production line, the hook number of the wire coil can be automatically tracked according to the failure information of the automatic cutting system, and the FRD card on the C-shaped hook can be identified by the card reader before the finished product cutting post of the P&F line, so as to achieve automatic alarm and reminder, and improve the stability of the quality operation of the finished product cutting process.
5、Closing remarks
The project from construction to commissioning about 4 months, although from the normal rolling mill rhythm of 3.5 seconds, there is a gap of 1.5 seconds, but compared with the initial commissioning of 15 seconds has made great progress. The success rate of automatic cutting from the initial commissioning 30% to about 90% now, and put into industrial normal production requirements is still a step away.
With the continuous improvement of material and living standards, the mechanization, automation and intelligent transformation of the steel industry with large workload, large physical labor intensity and high environmental temperature has become imminent. Today's rapid development of information technology and manufacturing technology has also created conditions for the transformation of these positions. The construction and application of the on-line automatic tail-cutting function of the high-speed wire rod production line.